Robot guide rail and robot positioner are two important components in industrial robotic systems. They offer several advantages that contribute to improved efficiency and productivity. Here are the advantages of each:
Robot Guide Rail:
- Enhanced Precision: Robot guide rails provide a fixed and stable track for the robot to move along. This ensures precise and repeatable positioning, resulting in accurate and consistent operations.
- Extended Reach: By using guide rails, the effective working range of the robot can be extended. The rail allows the robot to move beyond its regular reach, enabling it to access a larger workspace without the need for additional equipment or repositioning.
- Increased Payload Capacity: Guide rails can support heavy loads, allowing robots to handle larger and bulkier workpieces. This expands the robot’s capabilities and enables it to perform tasks that require higher payload capacities.
- Flexibility and Adaptability: Robot guide rails can be designed in various configurations, including straight, curved, or multi-axis paths. This flexibility enables the robot to navigate complex work environments, adapt to different production layouts, and perform tasks in confined spaces.
- Separation of Robot and Operator: Guide rails provide a physical barrier between the robot and the operator, enhancing safety in collaborative work environments. It helps ensure that humans and robots can work side by side without the risk of accidental collisions.
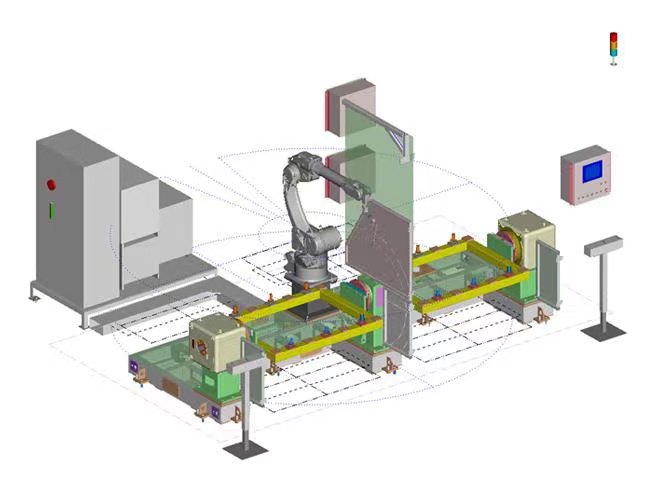
Robot Positioner:
Versatile Workpiece Positioning: Robot positioners enable precise and controlled manipulation of workpieces. They can rotate, tilt, or adjust the position of the workpiece to optimize the robot’s access and orientation during the manufacturing process. This versatility improves the efficiency and quality of operations.
Increased Throughput: Positioners allow for simultaneous or sequential processing of multiple workpieces. They can be programmed to automatically position and present workpieces to the robot, reducing idle time and increasing overall productivity.
Improved Ergonomics: Positioners can be used to position workpieces at ergonomic heights and angles, minimizing operator fatigue and discomfort. This ergonomic advantage enhances worker safety and contributes to a more efficient and comfortable working environment.
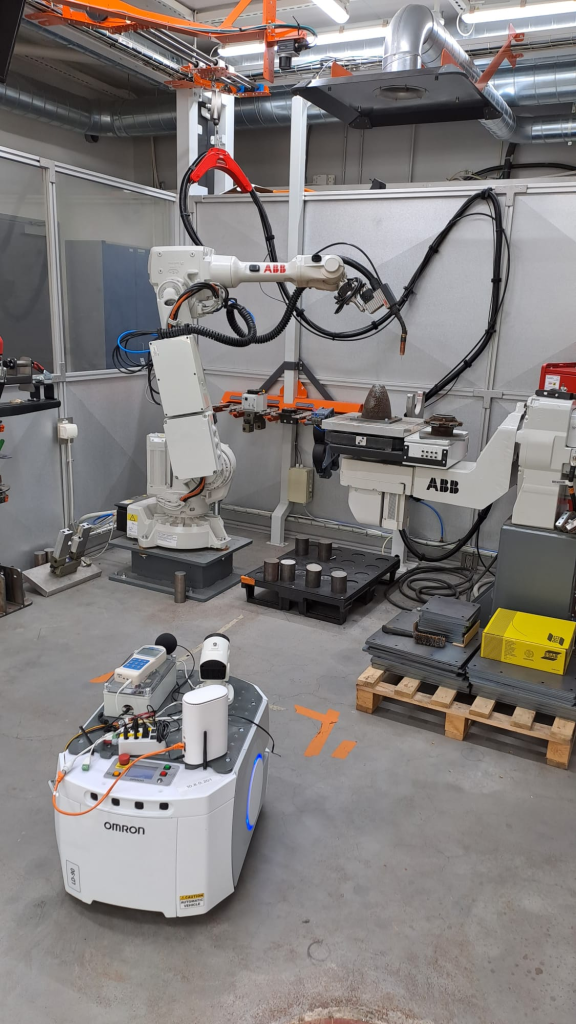
Easy Integration: Robot positioners can be seamlessly integrated into robotic systems. They are typically compatible with various robot models and can be synchronized with robot motion, enabling coordinated and synchronized movements for efficient operations.
Process Optimization: By precisely positioning the workpiece, robot positioners allow for optimized process parameters, such as optimal welding angles or consistent painting positions. This optimization leads to improved quality, reduced rework, and increased overall process efficiency.
Overall, robot guide rails and robot positioners offer enhanced precision, increased payload capacity, improved flexibility, and optimized workpiece positioning. By leveraging these advantages, industrial robotic systems can achieve higher productivity, improved quality, and enhanced operational efficiency.
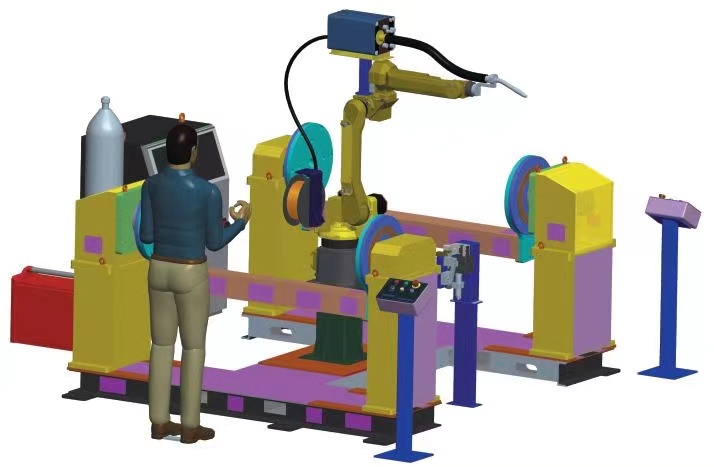
A Welding Positioner is an automated device used to transfer workpieces or adjust the position of workpieces during the welding process. By using a Welding Shifter, you can increase the efficiency of your work, and here are some of the ways to do it:
- Automated transfers: Welding variations can automatically transfer workpieces from one position to another, reducing the time and labor involved in manual handling. This saves time and increases efficiency.
- Precise positioning: Welding transposition machines are often equipped with an accurate positioning system that allows the workpiece to be precisely positioned in the weld position. This eliminates the need for manual adjustments and ensures accurate and consistent welds.
- Multi-station operation: Some welding transposition machines feature multiple workstations, allowing multiple welding tasks to be performed simultaneously. This reduces weld cycle time and increases productivity.
- Programmed control: Welding transposition machines can be programmed for control, allowing for pre-setting of weld paths, weld parameters, workstation switching, etc. This allows for automated continuous welding. This allows for automated continuous welding and increased efficiency.
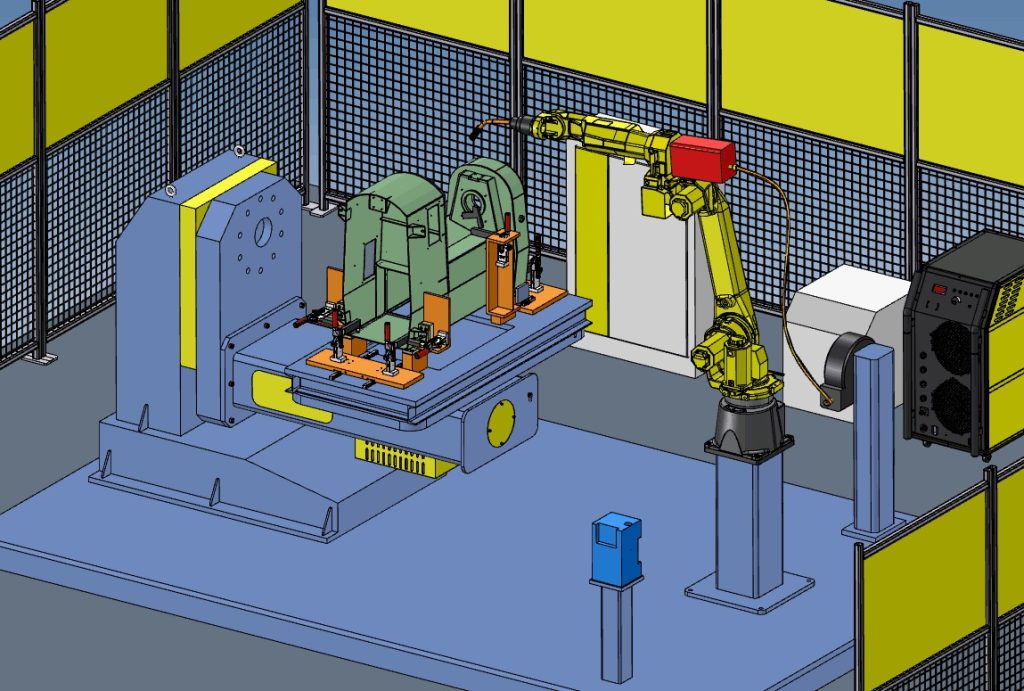
- Detection and feedback: Some advanced welding transposition machines have detection and feedback systems that monitor weld quality and make timely adjustments. This helps to reduce weld defects and the need for rework, improving overall efficiency.
- Increased production capacity: Through the use of welding transposition machines, mass production and continuous operation can be achieved, resulting in increased production capacity and efficiency.
It is important to note that in order to fully utilize the benefits of a Welding positioner, it is also necessary to plan the production process appropriately, carry out proper maintenance and servicing of the equipment, and train operators to be proficient in the use of the equipment.