Robot linear tracks offer numerous advantages in automation applications, providing enhanced flexibility, efficiency, and versatility. Here are some key advantages of incorporating robot linear tracks into your automation system:
1. Expanded Workspace: Robot linear tracks enable robots to move along extended linear paths, significantly expanding the workspace. This increased reach allows robots to access a larger working area without the need for multiple fixed robot stations. It facilitates the handling of larger workpieces or the ability to perform tasks in multiple locations, maximizing the utilization of the automation system.
2. Dynamic Path Planning: By integrating linear tracks, the robot’s path can be dynamically planned and adjusted. This flexibility allows for optimized motion trajectories, enabling efficient and precise movement between various workstations or production cells. The ability to adapt the robot’s path in real time ensures optimized cycle times and minimizes the risk of collisions or interference with other equipment.
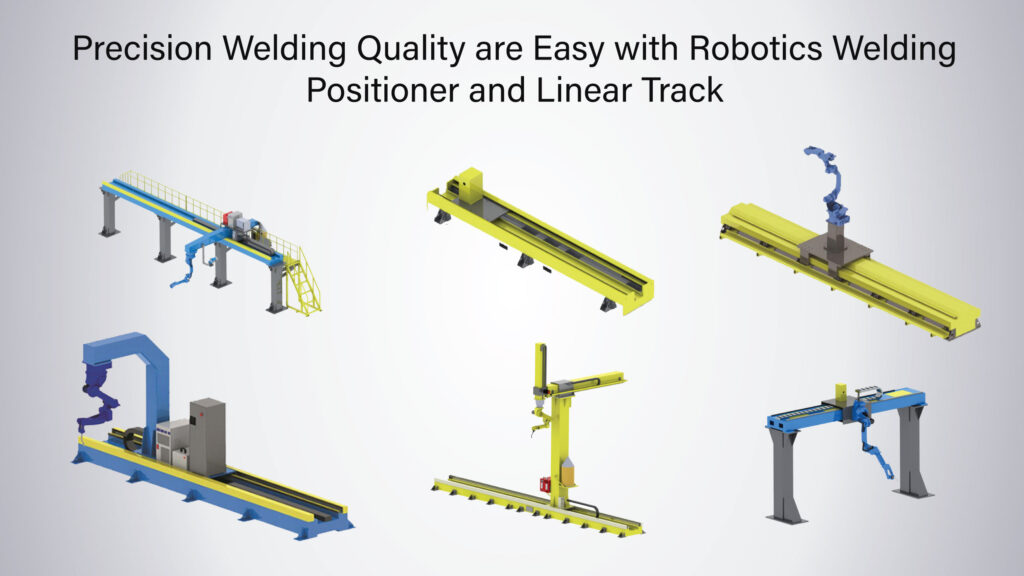
3. Multi-Station Operations: The robot track enables robots to serve multiple workstations or production cells along a linear path. This capability eliminates the need for separate robots for each station, reducing costs and simplifying the overall system design. One robot can efficiently handle tasks at different stations, improving productivity and reducing capital expenditures.
4. Increased Production Throughput: By utilizing linear tracks, the robot’s travel time between workstations is reduced, leading to increased production throughput. The continuous movement along the linear path eliminates idle time and enables seamless transitions between different production phases. This results in improved overall efficiency and higher output rates.
5. Flexible Layout Configuration: Robot guide rails provide layout flexibility in automation systems. The tracks can be configured in various arrangements, such as straight, curved, or branching paths, to accommodate specific production requirements. This adaptability allows for optimal utilization of available floor space and efficient integration with existing production lines or equipment.
6. Easy Integration with Robots: Linear tracks are designed for seamless integration with different robot models and brands. They typically feature standardized interfaces and mounting options, simplifying the connection and integration process. This compatibility ensures that existing or new robots can be easily incorporated into the automation system, enhancing scalability and ease of maintenance.
7. Precise Positioning and Repeatability: robot sliders offer high positioning accuracy and repeatability, allowing robots to precisely execute tasks. The tracks provide stable and controlled linear motion, ensuring consistent and accurate positioning of the robot at each workstation. This precision is vital for applications requiring tight tolerances or repetitive tasks.
8. Enhanced Safety Measures: Linear tracks often come equipped with safety features, such as sensors or emergency stop mechanisms. These measures help prevent collisions, detect obstacles, and ensure safe operation within the workspace. The integration of safety systems adds an extra layer of protection for operators and equipment, promoting a secure working environment.

High Load Capacity:
Robot sliders are designed to support heavy payloads, allowing the robot to handle larger objects or equipment during operation. This feature is particularly beneficial in industries that involve heavy-duty applications.
Smooth and Precise Motion: Linear tracks are engineered to provide smooth and precise motion control. They employ advanced mechanisms and bearings to minimize friction and ensure accurate positioning of the robot along the linear axis.
Multiple Length Options: Linear tracks are available in various length options to suit different workspace dimensions and requirements. This allows for customization and optimization of the track’s size to fit specific application needs.
Compatibility:
Robot linear tracks are designed to be compatible with different robot models and brands. They can be integrated seamlessly with various types of robots, offering versatility and ease of integration into existing automation setups.
Modular Design: Many linear tracks feature a modular design, allowing for easy installation and configuration. The track sections can be assembled and adjusted according to the desired length or layout, providing flexibility and adaptability.
Precise Positioning Sensors: Linear tracks often incorporate precise positioning sensors, such as encoders, to provide accurate feedback on the position of the robot along the track. These sensors ensure precise control and repeatability.
Safety Features: A
robot guide rail may include safety features such as emergency stop buttons, collision detection sensors, or safety interlocks to ensure safe operation and prevent accidents or collisions.
Integration with Control Systems: Linear tracks can be integrated with control systems and software, allowing for synchronized motion and coordination between the robot and the track. This enables seamless control and programming of the robot’s movement along the linear axis.