Choosing the right robot track system for your application is crucial to ensure optimal performance and productivity. A robot track system, also known as a mobile platform or base, provides mobility and movement capabilities to a robot, allowing it to navigate and operate in various environments. Here’s why and how you need to consider the selection of a robot track system for your specific application:
Enhanced Mobility:
Some applications require robots to move across different terrains or navigate complex environments. A suitable robot track system can provide the necessary mobility to traverse uneven surfaces, climb stairs, or operate in confined spaces. Assess the terrain and environmental conditions in which the robot will operate to determine the type of track system that can offer the required mobility.
Payload Capacity:
Consider the weight and size of the objects or equipment the robot will carry or interact with during its operations. The track system should have an adequate payload capacity to handle the required load without compromising stability or performance. Ensure that the chosen track system can support the maximum weight and size requirements of your application.
Speed and Agility:
Depending on the application, the robot may need to move quickly or maneuver with agility. Evaluate the speed and acceleration capabilities of different track systems to determine if they align with the operational requirements of your application. Consider factors like acceleration, top speed, and turning radius to ensure the track system can meet the desired performance criteria.
Power Supply and Endurance:
The track system’s power supply is crucial for continuous operation and endurance. Evaluate the battery capacity and estimated runtime of the robot guide rail system to ensure it can sustain the required operating time without frequent recharging or battery replacement. Additionally, consider the charging or refueling mechanisms and their compatibility with your operational setup.
Control and Navigation:
The robot slider system should integrate well with the robot’s control and navigation systems. Assess compatibility with the robot’s software and hardware interfaces, ensuring seamless integration and communication between the track system and the robot’s other components. This includes evaluating compatibility with sensors, control algorithms, and communication protocols.
Safety and Reliability:
Safety is paramount when selecting a robot’s external axis track system. Consider features such as collision avoidance, emergency stop capabilities, and fail-safe mechanisms to ensure safe operations in dynamic environments or when interacting with humans. Additionally, assess the track system’s reliability, maintenance requirements, and availability of spare parts to minimize downtime and maximize productivity.
Cost and Scalability:
Finally, consider the cost-effectiveness and scalability of the track system. Evaluate the initial investment, long-term maintenance costs, and the potential for scalability or future expansion of your application. It’s important to strike a balance between meeting your current operational needs and considering future growth or changes in requirements.
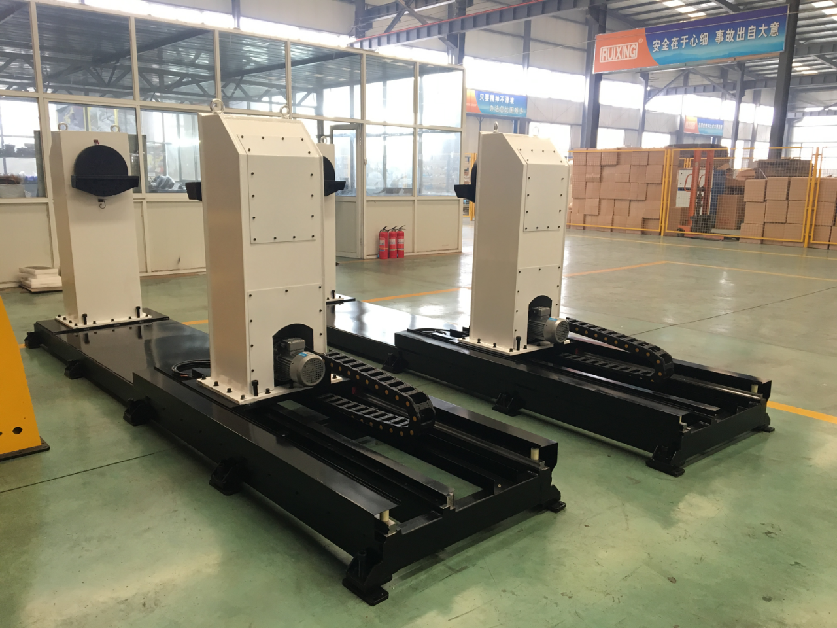
To make an informed decision, carefully analyze the specific requirements of your application and consult with experts or manufacturers who specialize in robot track systems. They can provide valuable insights and help you select the most suitable track system that aligns with your application’s needs, ensuring optimal performance, productivity, and return on investment.