WRS Robotics welding turntable systems for manufacturing
Part 1 Basic information about workpiece and description of welding requirements
1. Basic information about the workpiece to be welded
1.1 Name of the workpiece to be welded: bucket welding
1.2 The size range of the workpiece to be welded: 1500mm X750mmX800mm (subject to customer drawings)
1.3 The weight of the workpiece to be welded: less than 2000kg (according to the customer’s drawing)
1.4 Welding seam form of the workpiece to be welded: fillet joint, butt joint
1.5 Drawings of typical parts of the workpiece to be welded: (As shown in the figure, the specific dimensions shown are subject to the blueprint provided by the customer)
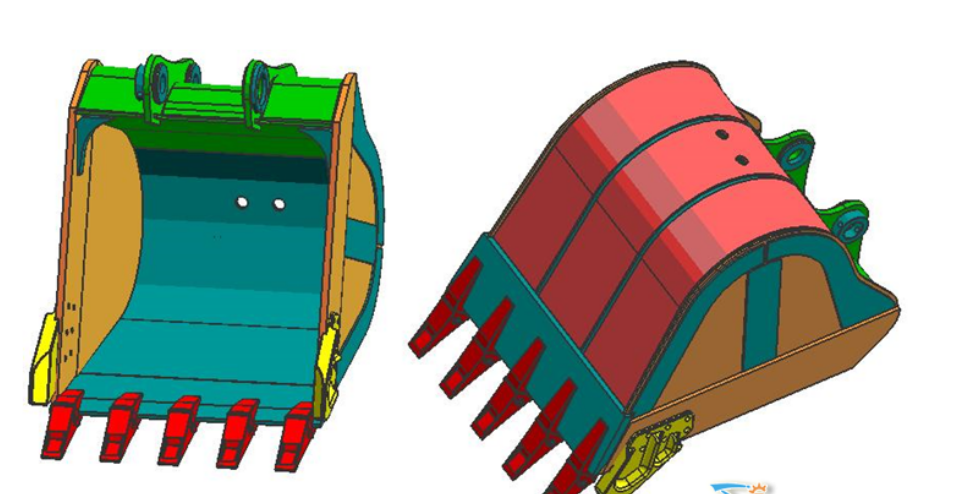
2. Welding process and process requirements
2.1 Workpiece loading and unloading method: due to the large and heavy workpiece, the workpiece loading and unloading adopts the hoisting method.
2.2 Welding process: Single wire 80%Ar+20%CO2 gas-shielded welding is used for welding. When welding, the workpiece is first manually assembled and spot-welded on the fixture, and then installed on the positioner of the robot workstation for robot welding. The welding quality can be tested by the buyer’s quality inspection department in accordance with China’s national standards or the buyer’s enterprise standards.
2.3 The robot is equipped with a KUKA cable external robot, and the welding power supply is equipped with a Fronius digital power supply for MAG welding.
Part II Introduction to Robotics Workstation
1. Brief description of the robot’s work:
This workstation adopts the welding method of a single robot and single station. Due to the distribution of the workpiece welding seam around the robot operating range is limited, so the welding workpiece will be placed on the robot and the coordinated movement of the positioner, the workstation mainly consists of an arc welding robot, welding power supply, welding sliding table, clearing gun shear.
The workstation mainly consists of an arc welding robot, welding power supply, welding displacement machine, moving slide table, clearing gun shear mechanism, system integration control cabinet, and so on.
2. Layout of the robot workstation: (the dimensions in the figure are for reference only)
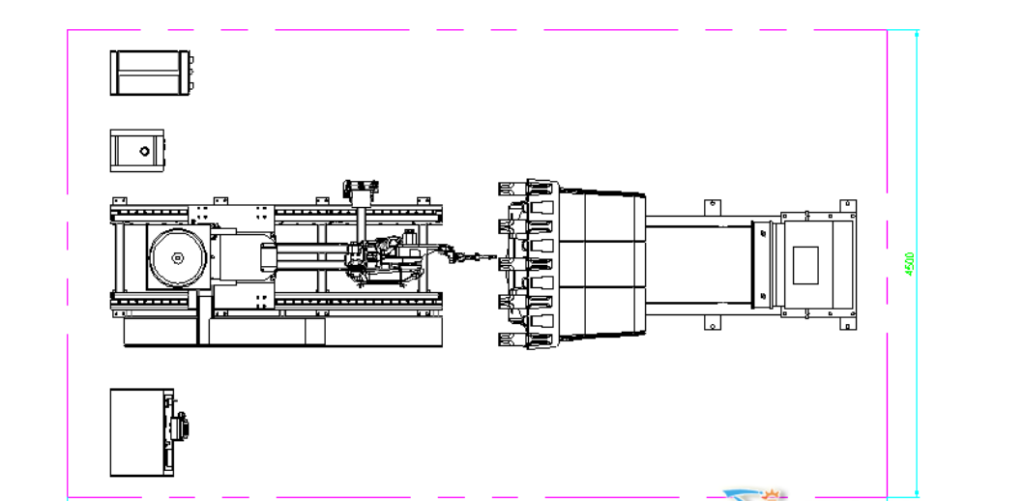
3. Rendering of robot workstation
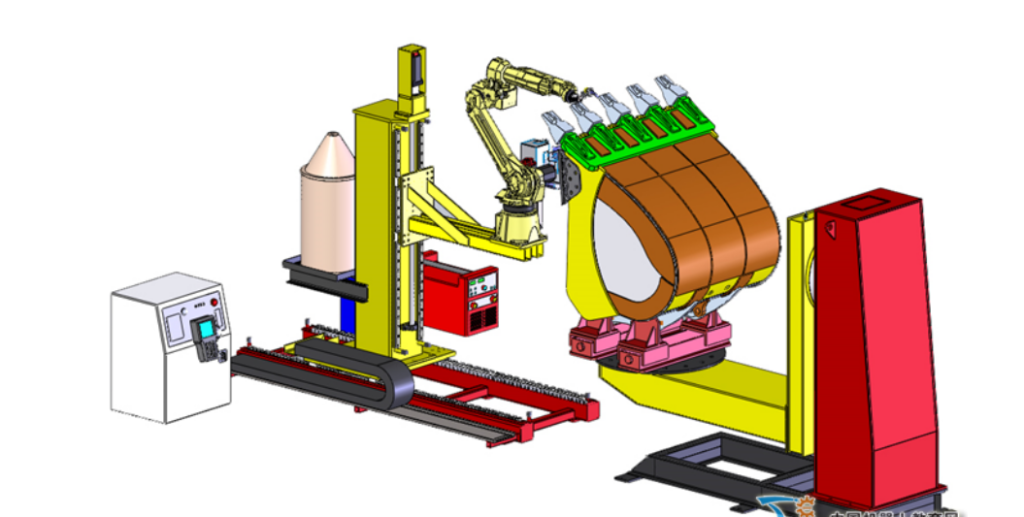
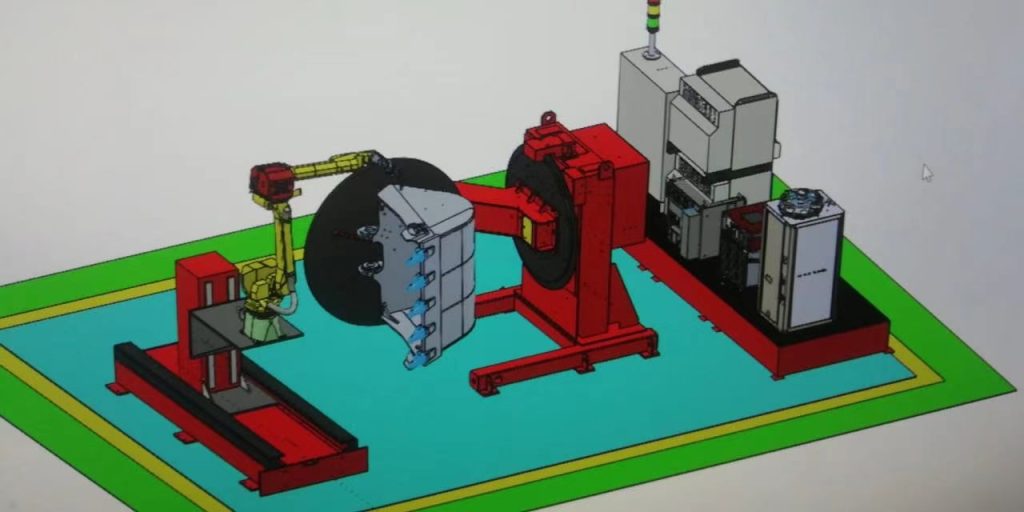
4. Robot workstation welding process
Hoist the bucket on the welding positioner→Start the robot→The arc welding robot starts to search→Arc welding (with arc tracking)→Single-step welding is completed→The robot goes to the next position for welding→The whole workpiece is welded by analogy→ for the next cycle. (The robot and positioner coordinate actions during the whole process)
Hoist the bucket on the welding positioner→Start the robot→The arc welding robot starts to search→Arc welding (with arc tracking)→Single-step welding is completed→The robot goes to the next position for welding→The whole workpiece is welded by analogy→ for the next cycle. (The robot and positioner coordinate actions during the whole process)
The third part is the main configuration table of the robot workstation
Robot welding system configuration list | ||||
No | Item | Specifications | Quantity | place of origin |
1 | Arc welding robot | KR 16 L6 | 1 | KUKA |
2 | Welding torch | TBI RM 80W | 1 | TBI |
3 | Anti-collision system | KS-1 | 1 | TBI |
4 | Torch cleaning station | HLQ-1 | 1 | RBT |
5 | Transformer | 5KVA | 1 | RBT |
6 | welding machine | TPS-5000 | 1 | Fronius |
7 | 2-axis welding positioner | 1 | RBT |
One-stop robot automation production solution expert
Robot automatic bucket welding workstation turnkey solution
Welding a bucket with a robot can be a precise and efficient way to ensure high-quality welds. Here are the general steps involved in welding a bucket with a robot:
Design and prepare the welding fixture: Create a welding fixture that securely holds the bucket parts in the correct position for welding. The fixture should provide stability and accessibility for the robot during the welding process.
Set up the robot and welding equipment: Position the robot and the welding equipment, such as a welding power source and wire feeder, in proximity to the welding fixture. Ensure that the robot is programmed and calibrated correctly for the welding task.
Prepare the bucket parts: Clean the bucket parts thoroughly to remove any contaminants, such as grease, oil, or debris. Proper cleaning ensures better weld quality.
Apply appropriate welding parameters: Set the welding parameters on the welding power source, including voltage, current, and wire speed, based on the material and thickness of the bucket parts. Consult welding procedure specifications (WPS) or the welding engineer for recommended parameters.
Program the welding path: Using the robot programming software, define the welding path and sequence. Consider factors such as joint access, welding direction, and weld bead overlap. Optimize the path to minimize unnecessary movements and maximize efficiency.
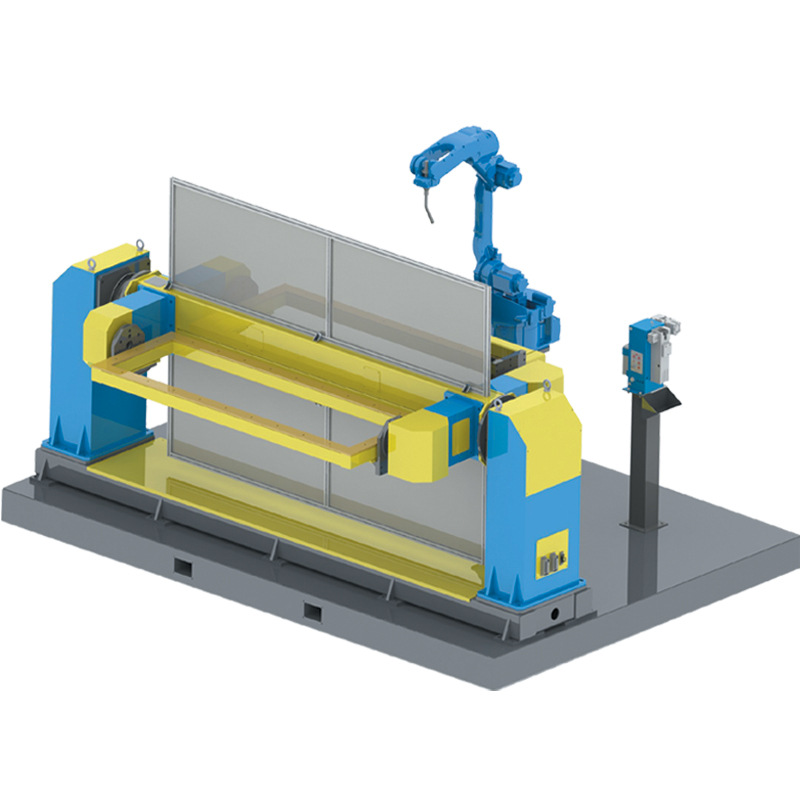
Perform a test run: Before executing the full welding operation, perform a test run to ensure that the robot follows the programmed path accurately and that the welding parameters are appropriate. Make any necessary adjustments to the robot program or welding parameters.
Execute the welding operation: Once the test run is successful, initiate the welding operation. The robot will follow the programmed path while the welding equipment applies heat to fuse the bucket parts together. Monitor the process to ensure proper weld penetration and quality.
Inspect and evaluate the welds: After completing the welding operation, inspect the welds visually and, if necessary, using non-destructive testing methods to ensure they meet the required quality standards. This step helps identify any defects or discontinuities that may require rework or repair.
Post-welding processes: Depending on the specific requirements, perform post-welding processes such as grinding, cleaning, and painting to complete the bucket fabrication.
It’s important to note that the steps provided are general guidelines, and specific procedures may vary based on the welding equipment, materials, and specifications involved. Always refer to the manufacturer’s guidelines, and welding codes, and consult with welding professionals for the best practices in welding a bucket with a robot.