As the manufacturing landscape evolves, the integration of factory delivery robots is becoming essential for streamlined operations and enhanced productivity. These innovative solutions not only optimize material handling but also reduce labor costs and improve safety within your facility.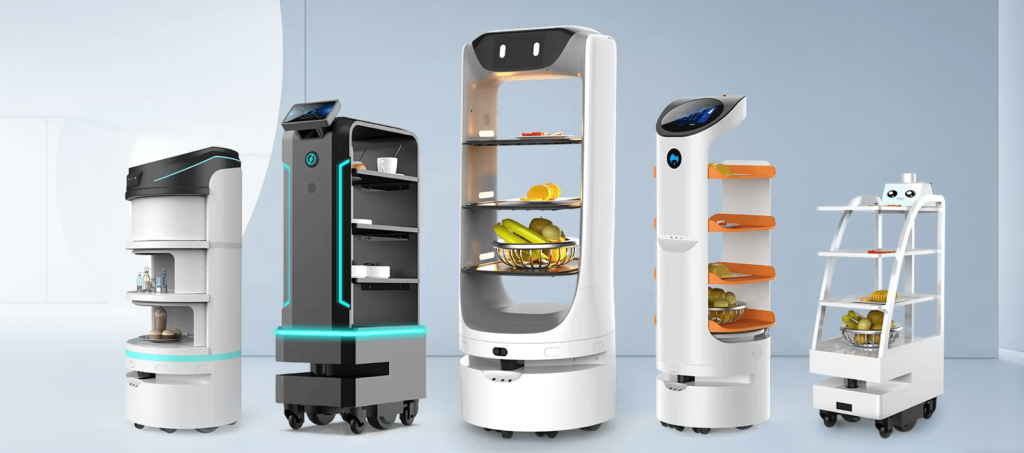
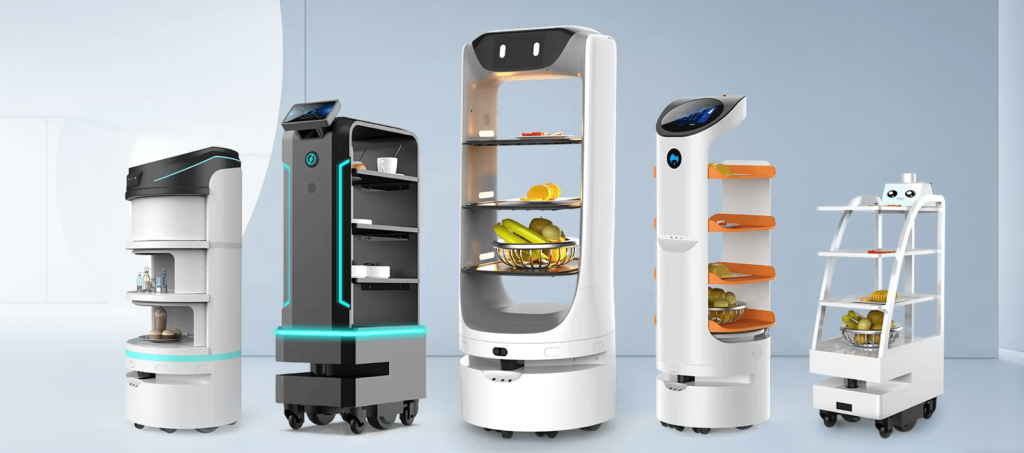
Ready to revolutionize your factory’s efficiency?
Discover how factory delivery robots can transform your workflow. From real-time tracking to seamless integration with existing systems, these robots are designed to meet the unique demands of your operations.
Factory delivery robots offer a range of benefits tailored to various manufacturing operations:
1. Increased Efficiency
- Automated Material Transport: Robots facilitate quick and reliable movement of materials, reducing downtime and manual handling.
- Real-Time Tracking: Enhanced visibility of inventory and workflow, allowing for better planning and resource management.
2. Cost Savings
- Reduced Labor Costs: Automation minimizes the need for manual labor in repetitive transport tasks, lowering overall payroll expenses.
- Lower Operating Costs: Efficient routing and operation reduce energy consumption and maintenance costs over time.
3. Improved Safety
- Minimized Human Error: Robots execute tasks with precision, reducing the risk of accidents associated with manual handling.
- Enhanced Workplace Safety: By handling hazardous materials or operating in unsafe areas, robots keep human workers out of harm’s way.
4. Flexibility and Scalability
- Adaptable to Different Layouts: Robots can navigate various factory layouts, making them suitable for both large and smaller operations.
- Scalable Solutions: As production demands increase, additional robots can be integrated easily without significant disruptions.
5. Enhanced Productivity
- 24/7 Operation: Robots can work continuously without breaks, significantly increasing throughput.
- Faster Delivery Times: Streamlined transport processes lead to quicker turnaround times for production cycles.
6. Data Collection and Analysis
- Operational Insights: Robots can collect data on material flow, helping manufacturers identify bottlenecks and optimize processes.
- Predictive Maintenance: Continuous monitoring allows for timely maintenance, reducing unexpected downtimes.
7. Better Space Utilization
- Compact Design: Many factory delivery robots are designed to fit into tight spaces, maximizing floor space efficiency.
- Dynamic Routing: Ability to navigate around obstacles and optimize paths contributes to better use of available space.
Conclusion
By integrating factory delivery robots, manufacturers can enhance efficiency, reduce costs, and improve safety while maintaining flexibility and productivity. Adopting this technology positions companies to thrive in an increasingly competitive landscape.
There are several types of delivery robots that are commonly used in factory and warehouse environments:
- Autonomous Mobile Robots (AMRs):
- These are self-navigating robots that can move materials and goods through the facility without the need for fixed tracks or rails.
- AMRs use advanced sensors, mapping, and navigation algorithms to plan and execute efficient routes.
- Examples include Fetch Robotics, MiR (Mobile Industrial Robots), and Autonomous Solutions Inc. (ASI) robots.
2. Automated Guided Vehicles (AGVs):
- AGVs are guided by magnetic strips, optical guidance, or navigation software to follow predetermined paths.
- They are typically used for repetitive, high-volume material transport tasks in structured environments.
- Examples include KUKA KMR iiwa, Balyo, and Jungheinrich AGVs.
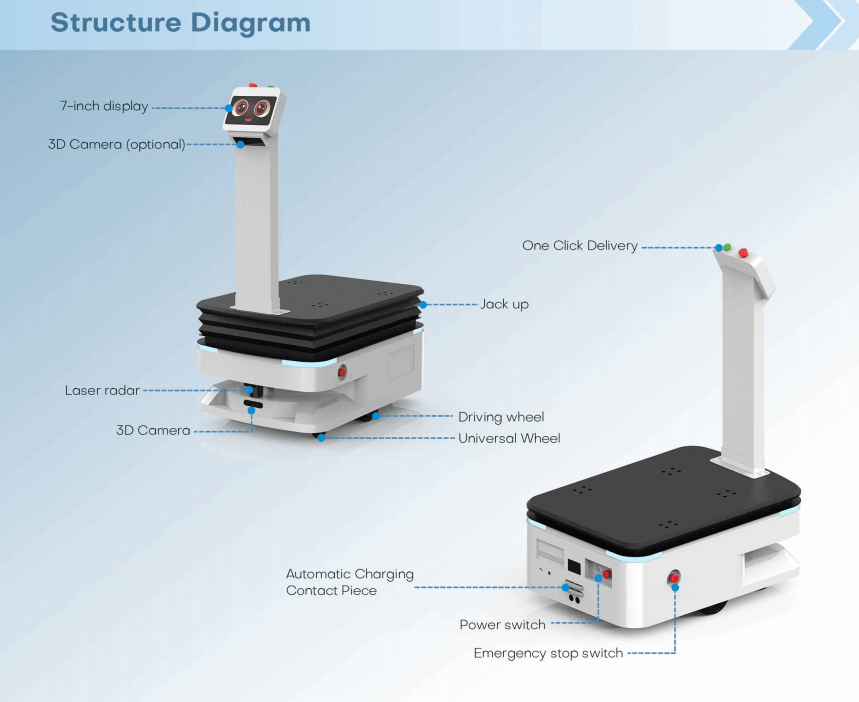
3. Collaborative Robots (Cobots):
- Cobots are designed to work safely alongside human workers, assisting with material handling and transportation tasks.
- They often have sensors and control systems that allow them to detect and avoid collisions with people and objects.
- Examples include Universal Robots, FANUC, and Yaskawa Motoman cobots.
4. Unmanned Aerial Vehicles (UAVs) or Drones:
- Aerial delivery drones are being explored for warehouse and logistics applications, particularly for moving items between storage areas and picking stations.
- These can quickly transport items vertically and horizontally, improving overall material flow.
- Examples include the Zipline drone and the Flytrex delivery drone.
5. Robotic Carts and Tuggers:
- These are wheeled robots designed to transport pallets, carts, or other material handling equipment through the facility.
- They can be programmed to follow specific routes or respond to pick-up and drop-off commands.
- Examples include the Vecna Robotics autonomous tugger and the Seegrid robotic cart.
- The choice of delivery robot type depends on the specific requirements of the factory or warehouse, such as the layout, material handling needs, and level of human-robot collaboration required.
Don’t wait—take the first step towards automation today!
Contact us to learn more about our factory delivery robot solutions and how they can be tailored to fit your specific needs. Schedule a demo and see firsthand the impact these robots can have on your production processes.
Contact us: www.wrsrobotics.com
Email:info@wrsrobotics.com